
Harvest RAMPs Up the Volume with a $1.65 million CEC Grant
Sonic Manufacturing is proud to announce our role as a Manufacturing Partner with Harvest.
Harvest has achieved so much in such a short time: strong sales, delighted customers, a Pod that keeps getting smarter – and lots of media and investor attention that allows us to decarbonize even more homes.
I’m especially proud today because the California Energy Commission awarded Harvest a $1.65 million RAMP grant to scale up production and deliver the smartest HVAC on Earth at a faster…
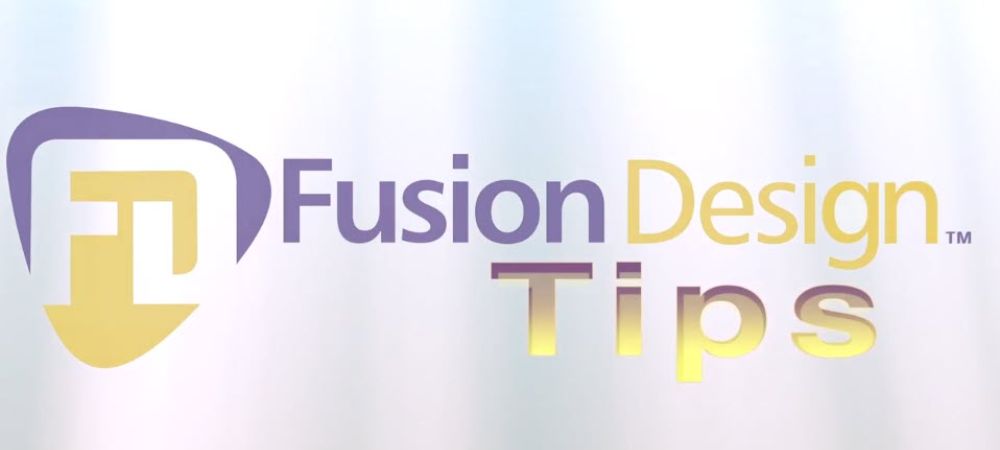
Our Partner Fusion Design
Based in Silicon Valley, Fusion Design (fusiondesigninc.com) is a leading product and equipment development consultancy with over 20 years of experience with Industrial Design, Mechanical Engineering. Fusion Design has done over 1200 projects – building ideas to reality. Fusion and Sonic have a long-standing relationship. Sonic is a partner for manufacturing high and low-volume production needs in all popular technologies.
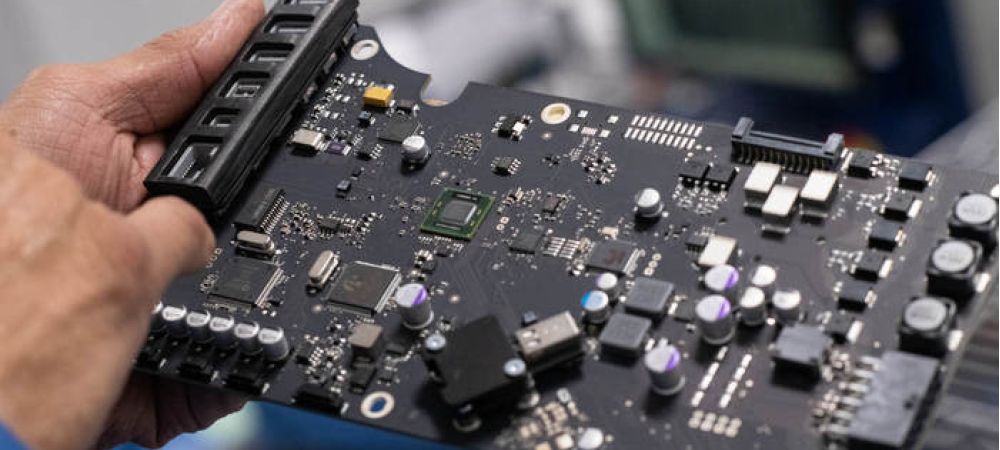
Cost Effective, Quick Delivery of PCBA’s
Written on . Posted in Articles of Interest, Blog, Component Sourcing, Manufacture, New Product Information.
With all the challenges facing the electronic manufacturing industry, cost and time as competitive strengths at Sonic Manufacturing Technologies help keep your business on a profitable track. Rising costs, long lead times, and access to talent are the chief concerns for product teams according to data from IPC.
In the IPC survey, respondents reported:
Rising material and labor costs are stifling profits and limiting growthInventories remain low due to electronic manufacturing supply ch…
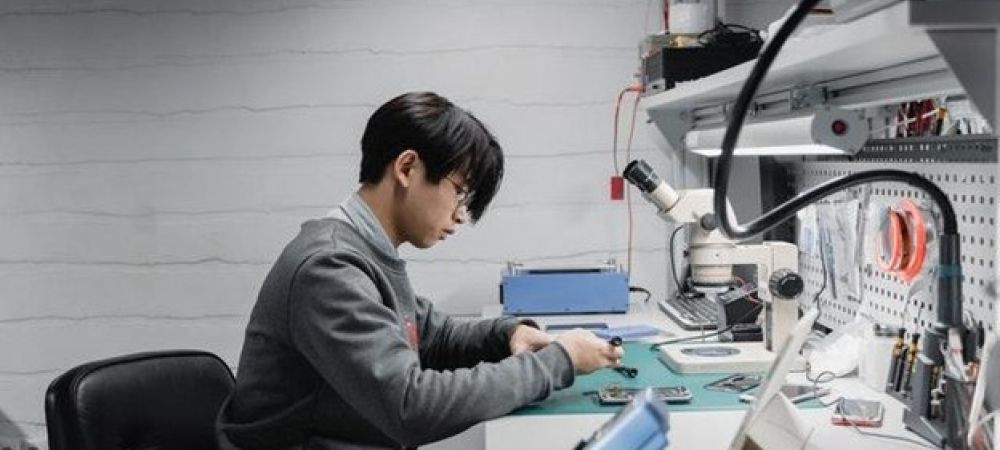
What Are the Benefits of Box Build Assembly
Box Build Assembly Services – What is Involved?
A box build assembly is an integrated system built around a printed circuit board (PCB) or set of boards and other modules. This system usually includes an enclosure and wiring, which are used to connect the box build to the next higher assembly. Enclosure design and materials are determined based on the application (indoor / outdoor for instance), heat signature (like for networking and servers) and usage (like personal wearables or tableto…

Sonic’s Supply Chain Difference
Written on . Posted in Articles of Interest, Blog, Component Sourcing, Manufacture, New Product Information.
Sonic’s supply chain difference is what sets us apart from other electronic manufacturing services companies in Silicon Valley. When we say that Sonic Manufacturing Technologies takes an agile approach to PCB and electronic manufacturing, we mean that we optimize every step in the product development lifecycle.
What is Sonic’s supply chain difference? It’s streamlining every step of the process, from PCB design and component selection to supply chain optimization using a network of global…