
How to Improve Quality Control in PCB Manufacturing
Quality control is crucial in the printed circuit board (PCB) manufacturing process, as it ensures the reliability, functionality, and performance of electronic devices. By implementing effective quality control measures, manufacturers can minimize defects, improve customer satisfaction, and reduce costly rework or product recalls.
Let’s discuss some of the key strategies we use to enhance quality control in PCB manufacturing. These practices ensure that you will get the high quality and …

Key Benefits of Outsourcing PCBA Services for Your Electronics Project
Outsourcing has become a prevalent practice across various industries, and the electronics manufacturing sector is no exception. One specific area where outsourcing can yield significant advantages is in printed circuit board assembly (PCBA) services.
By entrusting your PCBA needs to a reliable and experienced service provider like Sonic Manufacturing, you can unlock a range of benefits that positively impact your electronics project.
Let’s explore the key advantages of outsourcing PCB…

Factors to Consider When Choosing a PCBA Service Provider
Choosing the right printed circuit board assembly (PCBA) service provider is a crucial decision that can significantly impact the success of your electronics manufacturing project. With numerous options available, it’s essential to carefully evaluate and select a service provider that aligns with your specific requirements.
To help you make the best decision for your company, here are some key factors to consider when choosing a PCBA service provider. By taking these elements into account…
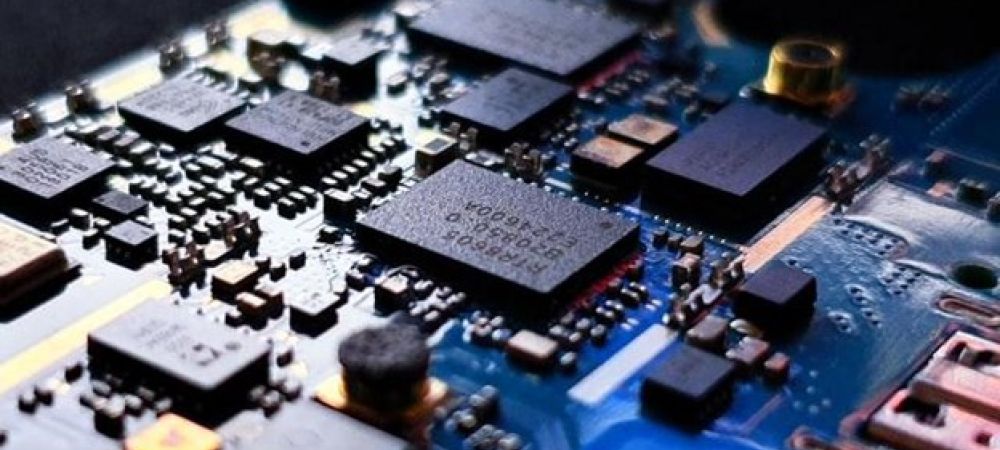
Tips and Tricks for Efficient PCB Layout
From the Experts at Sonic Manufacturing Technologies
Printed circuit board (PCB) design is an essential part of electronics design. Having an efficient design layout minimizes the chances of errors and reduces the chances of having to redo the board. Plus, a well-designed PCB layout lessens the probability of signal interference, EMI, and crosstalk.
Sonic Manufacturing Technologies understands the pressures to bring your products to the market quickly, which means there’s no room for e…

Partner with Sonic Manufacturing for Electronic Prototype Assembly Services
A prototype is an early sample, model or release of a product created to test a concept or process. It’s primarily used to evaluate a new design before a company invests in mass production. Prototypes often fail, and this shows designers where the defects are. The team then can ‘go back to the drawing board’ and refine the design. Prototypes avoid wasted time, money, and headaches and can even save lives.
In printed circuit board (PCB) design, a prototype is the first sample that’s built …
CALL FOR A QUOTE
(510) 580-8500
OR EMAIL:
Sales@Sonicmfg.com